
Logistyka na miarę przemysłu 4.0
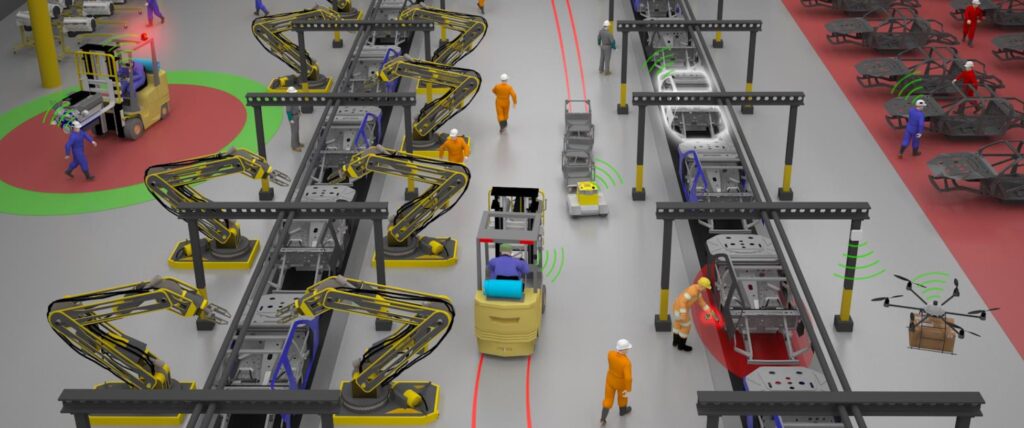
Artykuł ukaże się na łamach czasopisma PRODUCTION MANAGER 5/20
Coraz częściej standardem wśród firm działających zgodnie z filozofią Lean Manufacturing są wdrożenia rozwiązań z obszaru Industry 4.0. Wyzwania, jakie stawia przed nami obecna sytuacja takie jak, duża różnorodność wytwarzanych produktów, trudność za znalezieniem wykwalifikowanych pracowników, poszukiwanie bliżej zlokalizowanych dostawców, krótszy czas realizowanych zleceń wymagają wprowadzanie szeroko pojętych zmian i usprawnień. Wykorzystując narzędzia jakie daje nam nowoczesna technologia, możemy w odpowiedni sposób zoptymalizować procesy produkcji wykorzystując efekt synergii.
Konstrukcje modułowe, takie jak stanowiska montażowe, regały przepływowe (grawitacyjne) czy wózki transportowe są doskonale znane w większości zakładów produkcyjnych ( motoryzacja, lotnictwo, AGD, elektronika). Tego typu konstrukcje są często budowane w oparciu o system profili rurowych. Mogą być budowane i modyfikowane w nieograniczonym zakresie przez techników Lean Technology lub pracowników zakładu, dla którego powstają ( pod odpowiednim przeszkoleniu). Konstrukcje mogą być wykonane w systemie 28.0/28.6mm. Szeroka gama elementów umożliwia budowę szkieletów, które mogę być składowane na sobie. Dodatkowo zastosowanie zabezpieczeń w postaci kurtyn chroni składowane części przed kurzem oraz warunkami atmosferycznymi jak deszcz czy śnieg – w przypadku transportu z parkingu lub pomiędzy halami. Coraz częściej stosuje się konstrukcje wykorzystujące grawitację i kumulację energii (np. balansery) tzw. karakuri. W takich układach nie ma potrzeby stosowania zasilania zewnętrznego, a efekt np. windy, jest widoczny i znacznie ułatwiający pracę operatorom.

Regały przepływowe i stanowiska montażowe mogą być opcjonalnie wyposażone w systemy typu pick to light, pick by point itd., które poprzez zapalanie lampek lub podświetlanie obszaru ułatwiają pracownikowi pobranie odpowiednich komponentów i redukują popełniane błędy.
Aby odpowiednio zaprojektować linię montażową należy szczegółowo przeanalizować proces montażu m. in. analiza spaghetti. I tutaj bardzo pomocnym narzędziem jest system lokalizacji obiektów. Składa się on z nadajników oraz anten dzięki czemu możemy śledzić ruch obiektów w czasie rzeczywistym z dokładnością do 30cm. Generalnie obszar zastosowań jest ogromny m.in. przemysł (obszar produkcji i magazynowania), handel (ruch klientów w sklepach), sport (analiza ruchu i wydolności zawodników). W obszarze produkcji i magazynowania można wykorzystywać system m.in. do szeregu analiz ( spaghetti, ‘heat map’, aktywności), poprawy bezpieczeństwa (np. niebezpieczne zbliżenie się pracownika do wózka lub niebezpiecznej strefy), kompletacji (system nawiguje pracownika strzałkami wyświetlanymi na ekranie tabletu lub okularach).
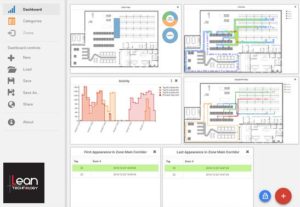
W obszarze magazynu oraz linii montażowych pracownicy mogą być wspierani przez strzałki wyświetlane na tabletach, smart watch’ach okularach AR itd. Po dotarciu do celu pobranie/dostarczenie może być potwierdzone poprzez zeskanowanie odpowiedniego kodu. Tego typu rozwiązania świetnie się sprawdzają w coraz bardziej popularnych sklepach internetowych, gdzie pracownicy kompletujący zamówienia są nawigowani przez system wyświetlający instrukcje na monitorze (tablecie) umieszczonym na wózku kompletacyjnym.
Kolejnym elementem ‘układanki’ są roboty AGV (automated guided vehicle) które bez udziału operatora transportują komponenty na terenie zakładu produkcyjnego lub magazynu. Najczęstszym zastosowaniem w przemyśle motoryzacyjnym jest transport z magazynu lub obszaru kompletacji (kittingu) na linię montażową w formie pociągu. AGV ciągnie za sobą wagoniki z komponentami a dostawy są realizowane najczęściej – redukcja stanów magazynowych na linii montażowej. AGV ofertowane przez firmę Lean Technology Poland występują w różnych wariantach konstrukcyjnych od tzw. ‘lokomotyw’, przez ‘tunele’, które podjeżdżają pod platformy i je transportują, a kończąc na systemach wyposażonych w elektrorolki, które automatycznie dostarczają i i odbierają elementy z platform za pośrednictwem komunikacji WIFI, a uciąg wynosi nawet do 2.000kg.

Aby zmniejszyć bufory, które są zlokalizowane w obszarze produkcji, niezbędne jest skrócenie czasu od momentu zamówienia komponentu przez operatora do czasu dostarczenia. W tym przypadku doskonale sprawdzają się rozwiązania typu E-Kanban. Różnego rodzaju czujniki mechaniczne, optyczne, wagowe są rozmieszczane m.in. na regałach przepływowych, pod paletami itd. Po przekroczeniu poziomu minimalnego, w ułamku sekundy za pomocą bezprzewodowej sieci 868Mhz magazyn jest informowany o konieczności dostarczenia odpowiedniego komponentu. Często komunikat jest uzupełniony o czas, na jaki wystarczy materiału na stanowisku. System może odpowiednio nawigować pracownika, tak aby trasa była najbardziej optymalna pod względem drogi jak i zapobiegnięcia ryzyka przestoju produkcji.

Podsumowując firma Lean Technology Poland oferuje kompleksowe rozwiązania i usługi (wsparcie merytoryczne, analizy optymalizacyjne, dobór odpowiedniego produktu, serwis) zgodne z najnowszymi trendami. Odbiorcami są zarówno małe innowacyjne firmy, które zdobywają rynek jak i duże międzynarodowe koncerny, które są światowymi liderami w swoich dziedzinach.